Despite repeated political promises recently saying otherwise, because of federal wants and big business needs over the last 100 years, the U.S. lacks both the low-cost labor and specialized manufacturing workforce needed to bring iPhone production home.
On Tuesday, White House Press Secretary Karoline Leavitt answered whether Trump believes iPhone production could ultimately move to the US. Allegedly, he thinks the U.S. has the money and labor to float such a project.
That is not the case.
To be clear, this isn’t just an Apple problem. This is a problem for manufacturing, especially electronics manufacturing, across the board.
However, with all the talk of how much these tariffs are going to make future iPhone models cost, let’s take some time to examine how this might affect Cupertino.
Made in China
When I was a child, nearly any time I turned over a knickknack or doodad, there’d inevitably be a little golden sticker on the bottom that said “Made in China.” At the time, I had no idea what that meant; I simply thought everything must be, and must have been, made in China.
And, as it turned out, I was half right. When I was born, the United States imported $4.77 billion in trade goods from China. Ten years later, in 1996, that number grew to, $51.51 billion, an increase of more than tenfold.
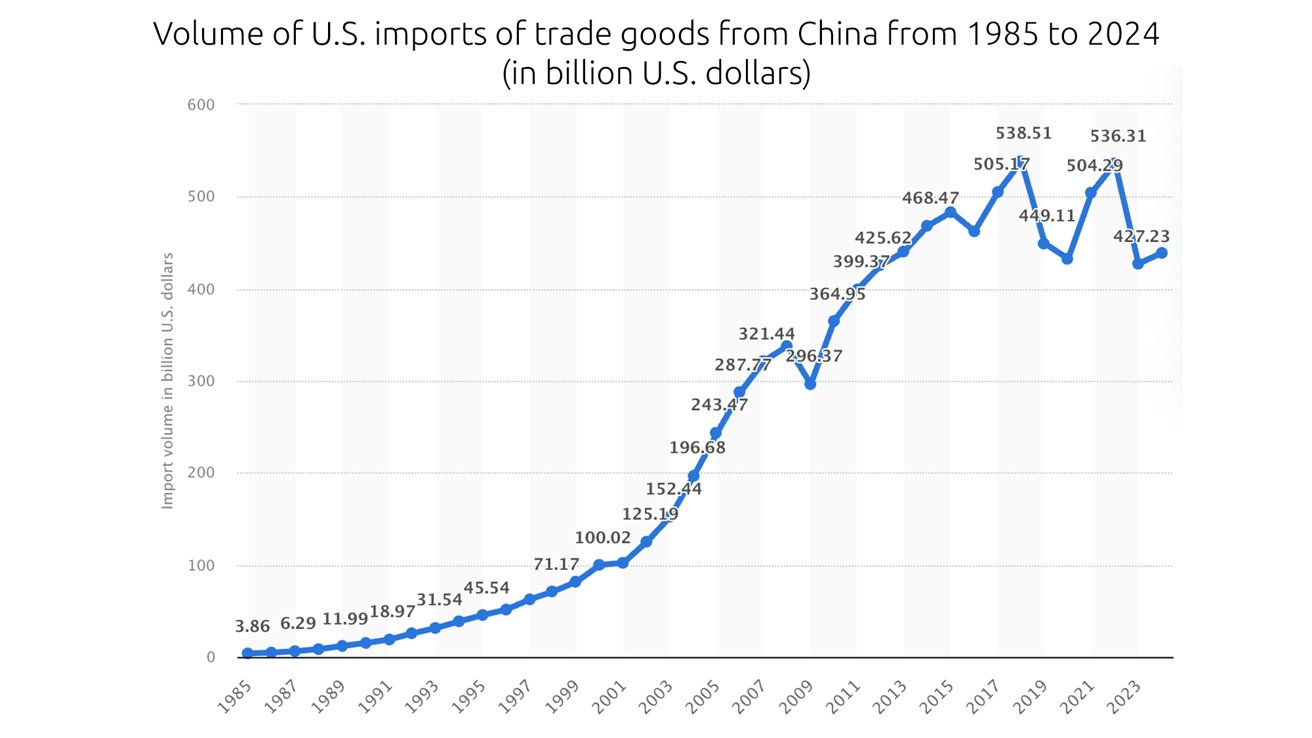
Image Credit: Statista Research Department
A little over two decades later, that number had grown more than tenfold again, reaching a staggering all-time high of $538.51 billion in 2018. That’s a lot of knickknacks and doodads.
All of this was encouraged by customer spending, US government initiatives, and big business need to appease investors by having eternal growth.
So, for as long as I’ve been alive, the U.S. has been steadily growing more dependent on China for its goods. Let’s take a look at how we got to this point, and how some decisions made decades ago echo to today.
400 Million Customers
America’s modern trade relationship with China was established in the 1930s. At that time, however, we weren’t looking to buy products from China, but rather to sell China our products.
NPR has a fantastic piece on the history of modern U.S.-China trade relations, but I’ll give you the broad strokes. Nevertheless, I suggest you check it out.
In the early 1910s, Carl Crow, a journalist, writer, and later on, businessman, moved to China to cover the country’s national revolution. During his time there, he realized that something far more lucrative awaited him: a career in advertising.
Crow went on to found Carl Crow Inc. in 1920. It was an advertising agency specializing in driving sales of American-made goods, like Buicks, Colgate toothpaste, and Kodak cameras to the Chinese market.
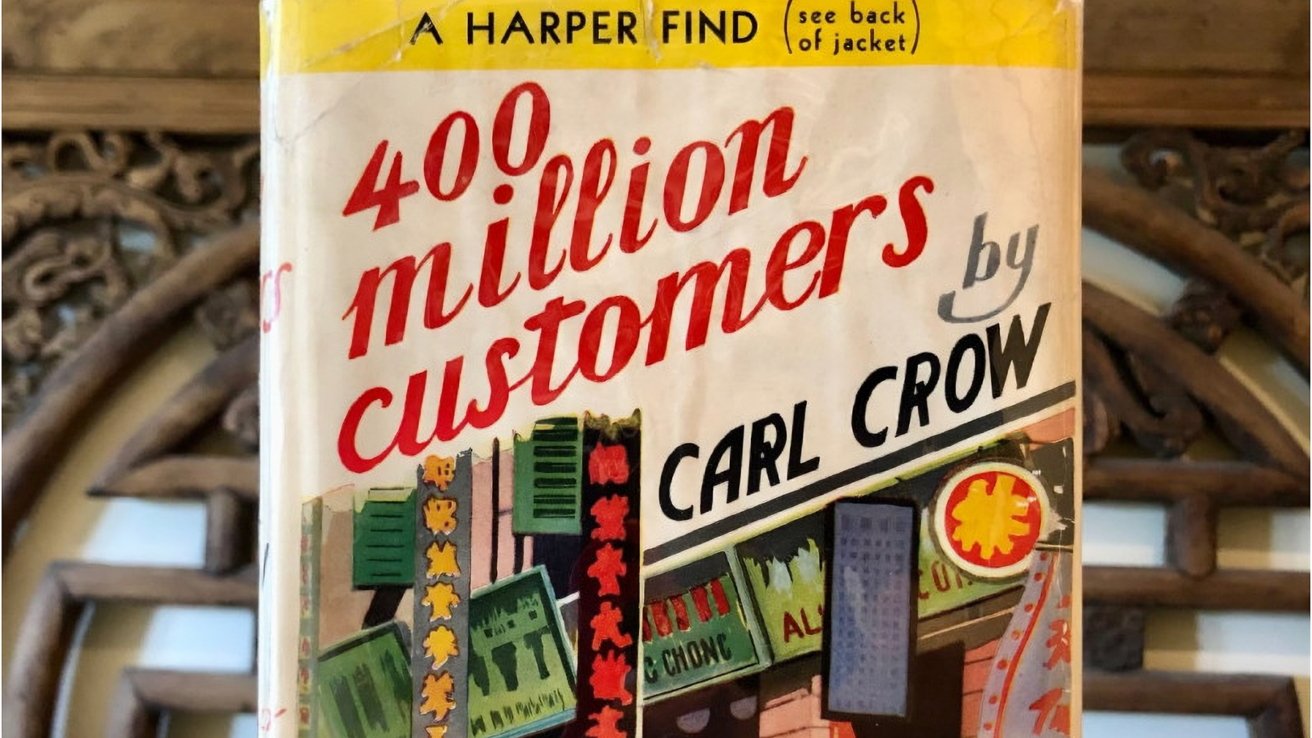
Image Credit: Katya Knyazeva (avezink) on LiveJournal
Crow did quite well, and in 1937 wrote a book called 400 Million Customers: The Experiences — Some Happy, Some Sad — of an American in China and What They Taught Him. Not only was the book an award-winning bestseller, it also opened America’s eyes to the idea of selling large quantities of goods to a then-mostly untapped market.
However, things quickly went askew, as they often do. In 1938, the “War of Resistance” between China and Japan made trade far more difficult.
In the following decade, the Chinese Communist Revolution took place. Then, between the Cold War and the war in Korea, the U.S. decided to slap China with a strict trade embargo in 1950.
800 million workers
It would take two more decades before the tensions between the U.S. and China eased, but things began to calm down in the 1970s. Slowly, China-made goods trickled into America. Some of the first goods were luxury-made textiles, spurred by America’s recent fascination with East Asian culture.
It didn’t take long before American businesses saw a new use for China: millions of workers willing to work for a fraction of what domestic labor costs. It also didn’t hurt that container shipping had been doing quite well for itself by that point.
Much like the textile workers of 1800s England came to fear and hate the automation and industrialization spurred by stocking frames, American textile workers pushed back against China-made goods.
Yet, by the 1980s, many American businesses — including Apple — had already begun outsourcing work.
A corporate symbiotic relationship
Throughout the ’80s and ’90s, most of Apple’s products were still made in America. But a fortuitous relationship between Apple and Taiwan-based Foxconn began to blossom in the late ’90s, and would ultimately lead to the situation Apple finds itself in today.
Foxconn is the world’s largest electronics manufacturer and has twelve factories scattered across China. While around 95% of iPhones are assembled in China, Foxconn unquestionably assembles the most iPhones — about 70%.
It was a long road to get there, but one that would tether Apple to China for the foreseeable future.
One year after he took the reins as Apple CEO, Tim Cook made a trip to Foxconn’s newly built Zhengzhou Technology Park — which is now often referred to as “iPhone City.” At that time, the facility employed roughly 120,000 people.
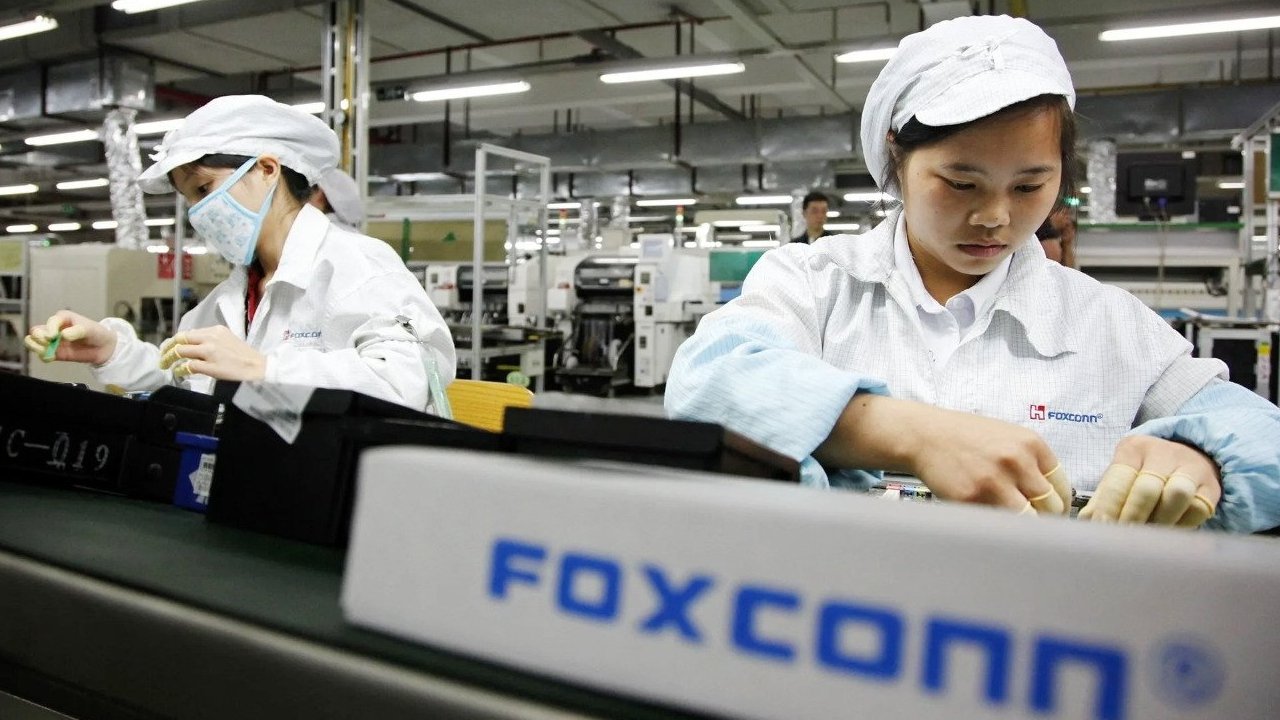
Workers in a Foxconn factory
That number would grow to 200,000 in 2022. It’s hard to say if Apple is the reason Foxconn is so successful, or if it’s the other way around. Likely the answer is somewhere in the middle, as it’s been wildly profitable for both businesses.
And Foxconn is hardly the only foreign company that Apple is inextricably bound to. The Taiwan Semiconductor Manufacturing Company, or TSMC, makes the semiconductors Apple uses in its products.
As a result, Apple accounts for the most significant portion of TSMC’s annual revenue — about 25.2%.
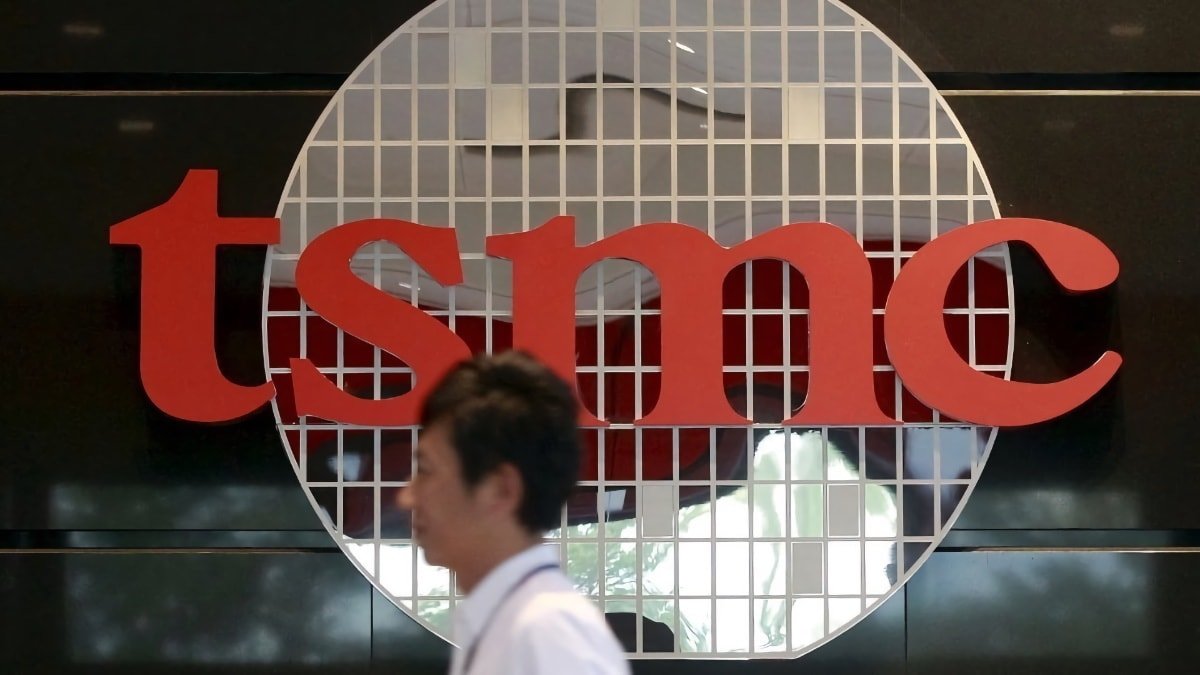
TSMC
And while TSMC does have a plant in Arizona, it wasn’t until September 2024 that it began producing chips. In fact, TSMC’s Fab 21 was beset with issues from the very start.
Unfortunately, TSMC’s second Arizona plant seems to be facing similar issues. That’s why most of TSMC’s chips, including those in the Apple Silicon lineup, are still manufactured in Taiwan.
Samsung Display, based in South Korea, is the primary supplier of iPhone and iPad displays. Its production plants are based in China, Vietnam, and India.
Virtually every part of Apple’s supply chain is tied to countries hit hard by the Trump Administration’s tariff plan.
There is no ‘pulling out’ of China.
Some may ask why Apple doesn’t just build its factories here; after all, the company has shown that it’s at least somewhat amenable to the idea of putting factories on US soil. Presumably, that would solve all of this trade war business.
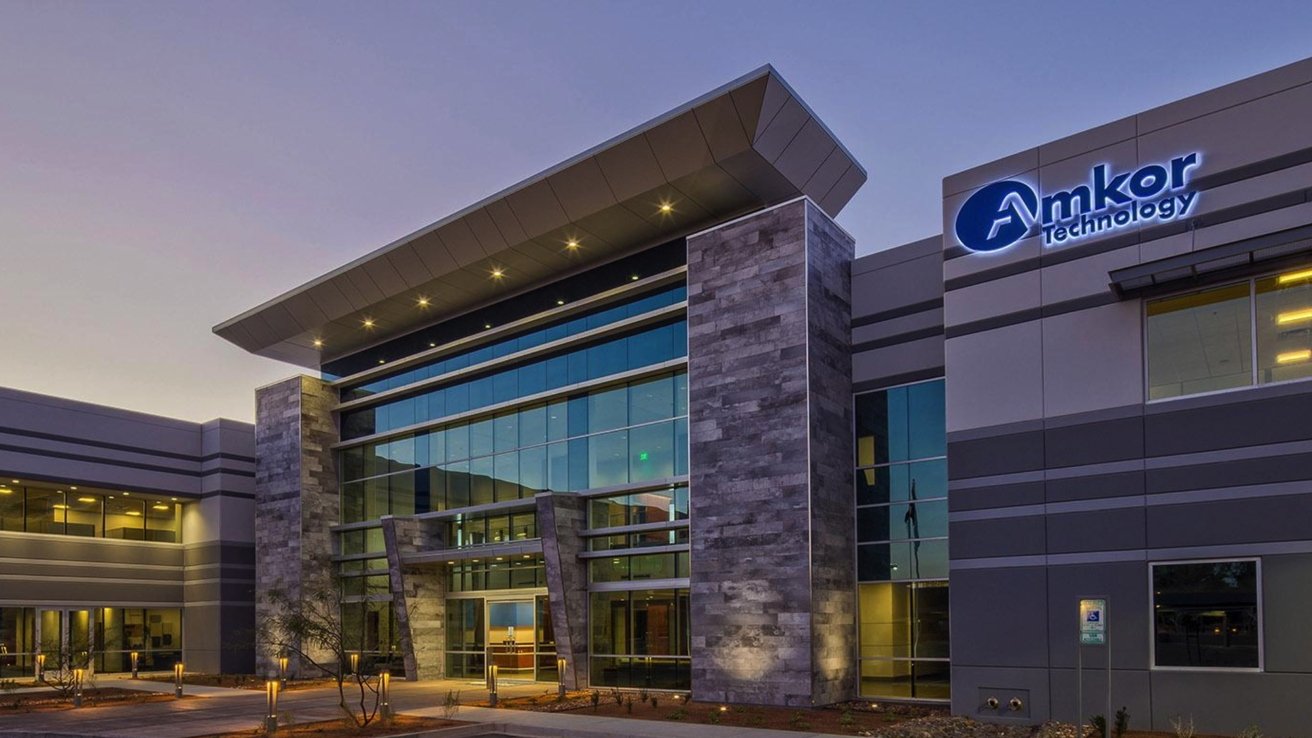
Amkor’s headquarters in Arizona
There’s a glaring problem behind that and one that likely cannot be solved easily, if at all.
For better or worse, Apple is primarily a provider of physical goods.
Sure, the tech giant has Apple Music, Apple TV+, Apple News, Apple Fitness+, the App Store — any of the digital services that it provides. And yes, Services profits have been growing steadily in the past several years.
In 2024, Services accounted for 25% of Apple’s $391 billion revenue — not too shabby.
However, the iPhone still makes up 51% of that revenue, or $201.2 billion. And Mac, iPad, Apple Watch, HomePod, and AirPods make up 24% — almost just as much as Services.
If Apple were suddenly unable to sell physical goods at a decent profit, it would be a devastating blow to the company. Possibly even one that it would not survive — and that’s before it attempted to build new factories in the U.S.
Dan Ives told CNN that it would take about $30 billion and three years for Apple to move its global supply chain back to American soil.
But with what money is it expected to do this — the money from Services? That seems highly unlikely.
And even if Apple did manage to build these factories on a reasonable time scale with what money it could hurriedly scrape together, it would still need to solve its biggest problem: domestic labor.
Human beings screwing in little, little screws
In America, we, at least for the time being, have something called federal minimum wage. While you can certainly argue that it’s not a living wage, it’s still a wage that employees are guaranteed.
Foxconn pays the average factory worker somewhere around $3 per hour, and expects them to work for ten to twelve hours a day. That means the factory is paying each worker, on average, $30-$36 per day. There are some opportunities to earn overtime, but even still, the cost of labor is relatively cheap.
American factory workers who went in at federal minimum wage, which is $7.25 per hour, would receive $58 if they worked a full 8-hour day. If they were expected to work 10 to 12 hours each day, the factory would need to pay them an additional $21.76-$43.52 in overtime.
And, if these factory workers lived in one of the 34 states and territories that have state wages above federal minimum, it’d only get more expensive. Arizona, for instance, has a state-set minimum wage of $14.70, making an 8-hour day cost $117.60.
So, either the factory needs to compromise on hours or compromise on money. Of course, that assumes you’d get American workers into a factory for minimum wage.
No one in America is going to assemble iPhones for minimum wage. I’d be willing to bet you’d be hard-pressed to find someone willing to do it for $15 or $20 per hour.
Factory work is tedious, at best. It is relentless, brutally dangerous, and lonely at worst. Some of you who have been following Apple as a company for at least a decade or so probably remember the string of worker suicides that primarily took place in 2010.
And, culturally, East Asia expects quite a bit more out of their average worker. In 2021, Vietnamese workers were asked to live on-site to help prevent the spread of Covid-19. They slept in little tents on the floor of the factory.
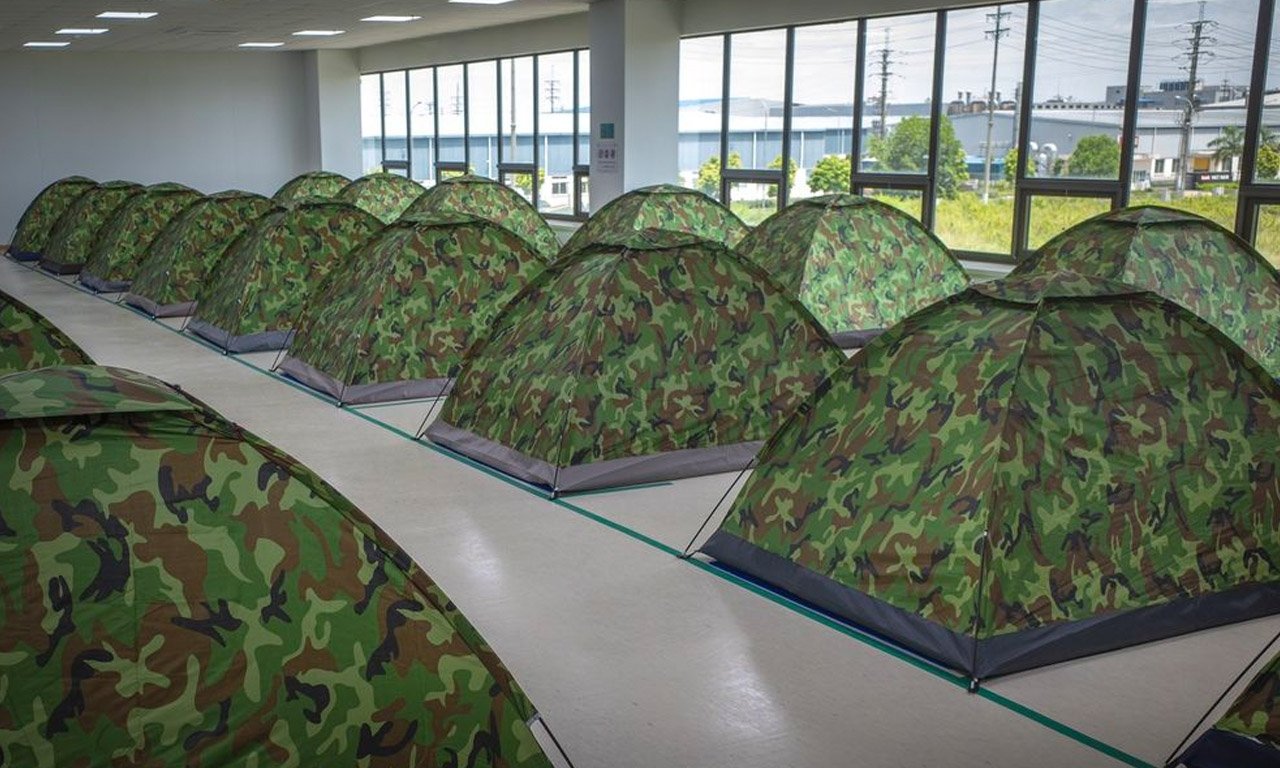
Vietnamese factory workers slept on the floor in tents | Image Credit: Giang Son Dong/Giang Son Dong
Americans do not typically work jobs that see them doing the same task, in and out, for eight hours a day. This is not something our culture has normalized in the last several decades.
And, even when Henry Ford did it, workers didn’t exactly love it either. And that’s despite Ford paying wages well above what the average worker could expect elsewhere as part of his Five Dollar Day program.
At $7.25 per hour, you can easily find more gainful employment elsewhere. And even at $15, you can likely find the same employment working as a cashier in nearly any national chain grocery store.
And, odds are, you’re probably not going to be asked to sleep on the floor of your local Aldi to prevent a temporary store closure.
Of course, Commerce Secretary Howard Lutnick recently and enthusiastically told CBS’ Face the Nation that Americans would have “the greatest resurgence of jobs in the history of America to work on these high-tech factories, which are all coming to America.”
He said that “the army of millions and millions of human beings screwing in little, little screws to make iPhones, that kind of thing is going to come to America.” He then followed it up by saying, “It’s going to be automated.”
He then noted that the factories would need HVAC technicians, electricians, and tradespeople to help keep everything running smoothly. While that is true, it’s putting the cart before the horse a bit.
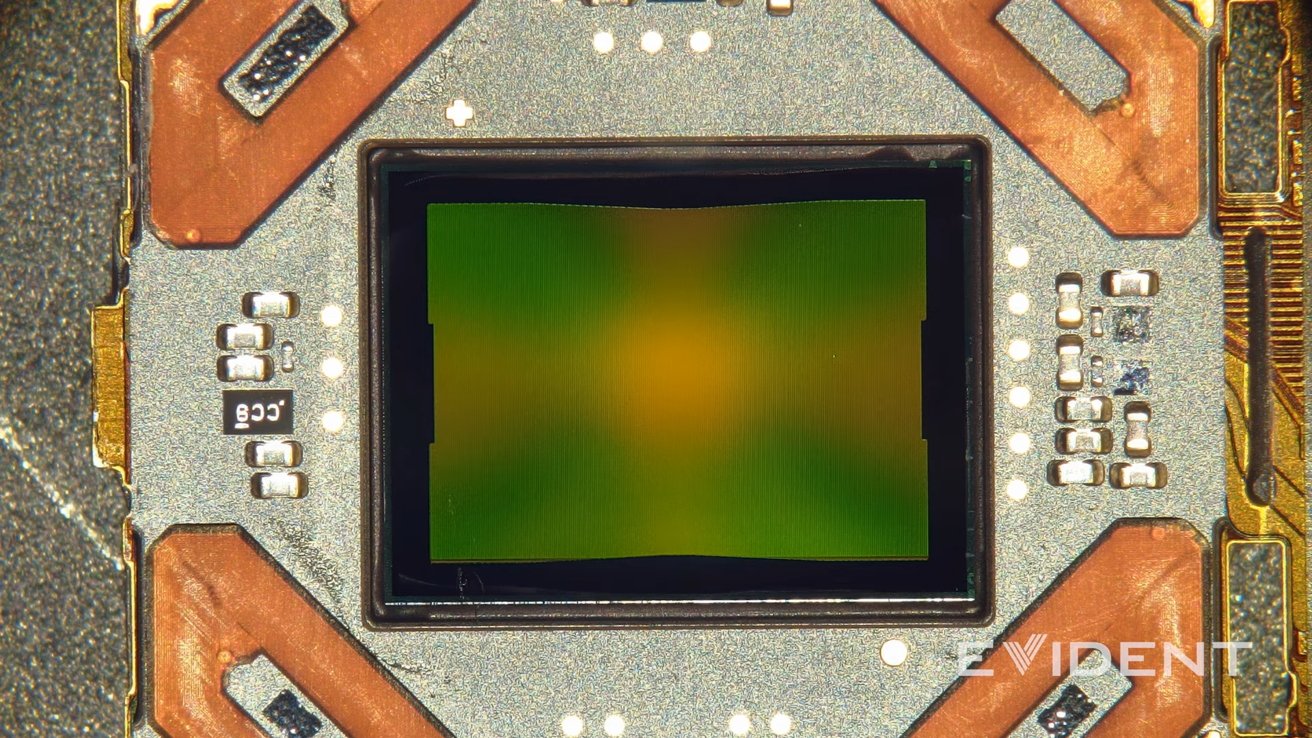
Image Credit: iFixit
Currently, iPhone production and assembly are not automated much, if at all. And while Apple has plans to wade into automation, with the end goal of reducing the number of workers in factories by 50%, it’s not there yet.
As it turns out, those little, little screws still need that army.
Factory work is hardly low skill
In America, we have the ugly habit of assuming all manual labor is low-skill. We tell our kids to do good in school and get a degree in college so they don’t become ditch diggers — and as the daughter of a one-time ditch digger, I take pretty big offense to that.
But you know who doesn’t have that outlook? Tim Cook.
In 2018, Cook sat down with Fortune’s Adam Lashinky to discuss why people shouldn’t look at China-based labor as low-cost, but rather highly specialized. As it turns out, China has the U.S. beat in one key area: precision tooling.
Vocational training is not seen as taking the “lower path” in China, while many other countries have de-emphasized vocational trades. Because these trades are still considered worthwhile, China has a wealth of tooling engineers.
America, on the other hand, doesn’t have that many. In fact, I didn’t even know what a tooling engineer was, let alone how critical they are to product manufacturing until just now.
But there is someone who knows what tooling engineers are: Tim Cook.
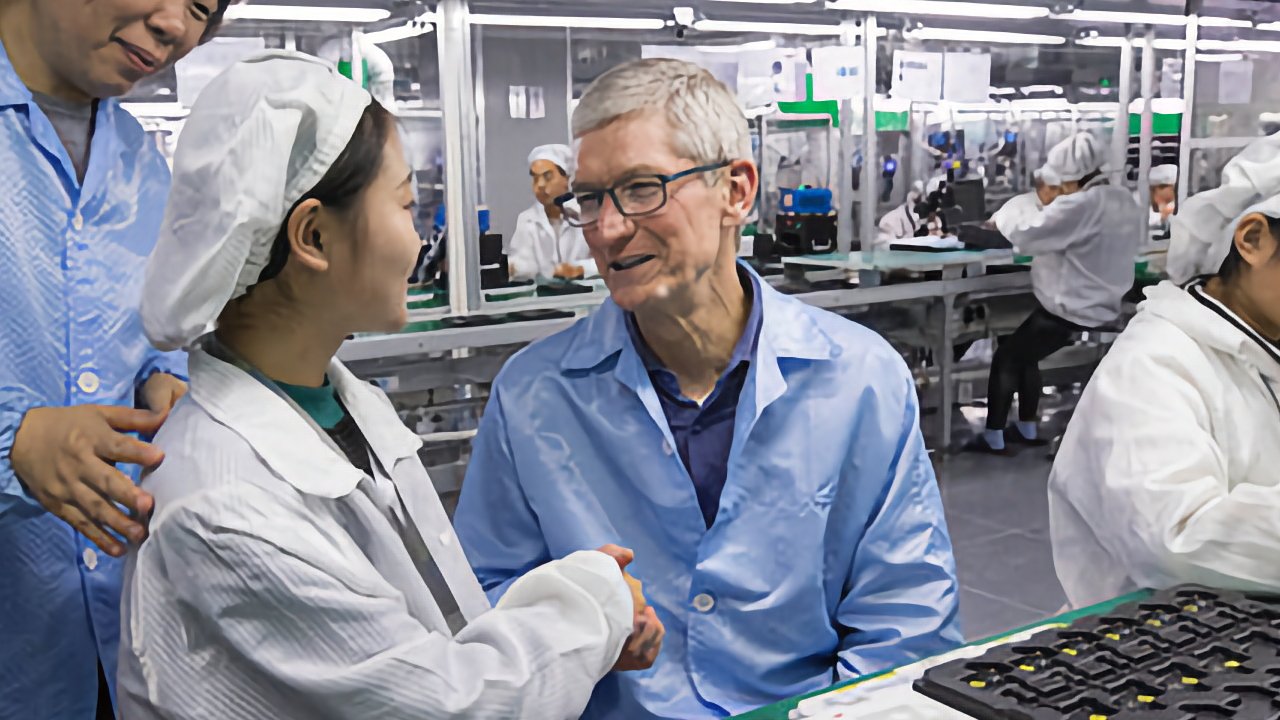
Tim Cook visits Luxshare factory in 2017. Source: Apple
“The products we do require really advanced tooling. And the precision that you have to have in tooling and working with the materials that we do are state-of-the-art,” Cook said in the interview. “And the tooling skill is very deep [in China].”
“In the U.S. you could have a meeting of tooling engineers and I’m not sure we could fill the room. In China you could fill multiple football fields.”
Tooling engineers are highly specialized workers who fall somewhere between craftsmen and traditional mechanical and electrical engineers. It’s very much an engineering job, but it’s also a job that requires an eye for design and a keen sense of problem-solving.
It’s also a very long educational process for just the training, much less the experience that Apple will need. This is literally a skill that will require a generation to fill in the quantity that Apple will need.
China has been honing this skill for decades to meet the demands of its trade partners. They aren’t innate skills, aren’t easily transferrable to robots, or are quickly taught to people who have no experience in manufacturing at the scale Apple needs.
And, China literally does not let them leave the country.
So, while it is possible that Apple could open factories in the United States, it’s not as easy as telling Apple that it needs to do it soon. And it’s certainly not made easier by jacking up the cost of materials now.
Even if it had the money to do so, and even if it got the workforce to agree to it, American factories would still manufacture products slower and at a lower quality, at least until Americans get an eye for this kind of manufacturing.
Even so, that doesn’t change the fact that a domestically produced iPhone would likely be prohibitively expensive. I’m a bit skeptical that we’d see prices jump to $100,000 per iPhone, but $3000 is in the realm of possibility given 145% tariffs on China now, and the reality of US labor and the costs to build that capacity out going forward probably 10 years.
Apple will likely continue to increase manufacturing in the U.S. in the future, that’s almost for certain. It is not a short-term thing, and if it happens at all, it will take probably six years at a minimum for low-yield high-defect production.
But, to answer the question: is Apple going to make the iPhone in America?
As Needham analyst Laura Martin aptly put it, “I don’t think that is a thing.”